Solution Summary: Remote-controlled Exothermic Welding System
Description:
Exothermic welding systems are designed to create strong, durable electrical connections through a high-temperature chemical reaction between aluminum and copper or steel. This method is used in various industries, including electrical grounding, cathodic protection, and rail connections, providing a permanent and corrosion-resistant bond. A remote-controlled exothermic welding system allows the welding process to be initiated from a distance via a control unit, enhancing safety and convenience.
The traditional exothermic welding process involves placing welding materials in a graphite mold and igniting them with a flint gun. The resulting chemical reaction produces molten metal that flows into the mold cavity, creating a molecular bond with the conductors.
nVent ERICO Cadweld
A remote-controlled exothermic welding system, such as the nVent ERICO Cadweld (figure 1), provides a safer and more efficient alternative to traditional exothermic welding.
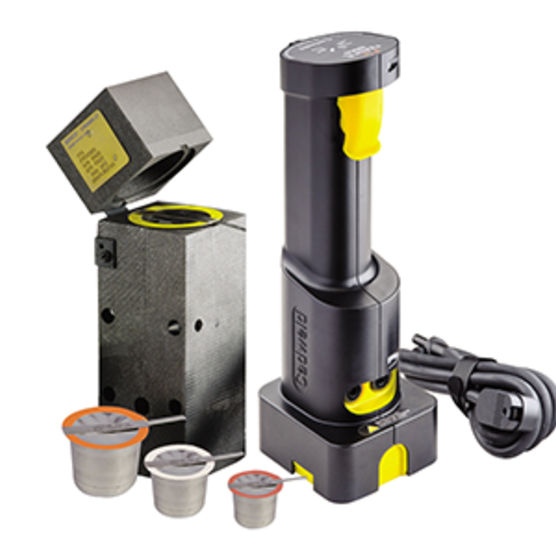
Figure 1. nVent ERICO Cadwell exothermic welding kit. (Photo courtesy of nVent)
To use this system, first prepare the materials and clean the conductors to ensure a strong bond. Place the conductors in a graphite mold and secure them. Compared to the traditional process, which requires manual mixing of ignition materials, the nVent ERICO Cadweld features a cup design with an integrated welding material package, streamlining the installation process.Then, using the remote control unit (figure 2), ignite the starting material from a safe distance. The exothermic reaction produces molten metal that flows into the mold cavity, creating a permanent bond between the conductors. Once the mold cools, open it and remove the welded connection.

Figure 2. A worker using the nVent ERICO Cadwell control unit to trigger the exothermic welding process. (Photo courtesy of nVent)
Risks Addressed:
Performing traditional exothermic welding in a confined space poses significant risks to workers. The process involves manually placing welding materials in a graphite mold and igniting them with a flint gun, which can generate hazardous fumes and consume oxygen in the confined area. This can lead to respiratory issues and potential oxygen deprivation.
Additionally, the close proximity required during ignition increases the risk of burns and other injuries from the high-temperature chemical reaction.
How Risks are Reduced:
A remote-controlled exothermic welding system mitigates confined space hazards by allowing the welding process to be initiated from a distance. This reduces the risk of respiratory problems, oxygen depletion, and burns, as workers are not physically present during the high-temperature reaction.
Further, the nVent ERICO Cadweld system utilizes a cup design with pre-mixed ignition material, enhancing safety by eliminating manual ignition material handling, reducing exposure to hazardous materials, and minimizing the risk of burns or chemical reactions. This also ensures a controlled and consistent welding process, decreasing errors and accidents, and improving overall worker safety.
Additional Considerations:
While remote-controlled exothermic welding systems enhance safety, it is essential for workers to adhere to all safety protocols, including wearing appropriate personal protective equipment (PPE) and following manufacturer guidelines.
Regular training and awareness programs can further ensure the safe and effective use of these systems.
Contributors:
Jean Christophe Le, MPH - CPWR The Center for Construction Research and Training
Availability
nVent
To obtain information, visit nVent ERICO Cadweld
or contact 1-800-248-9353 EFS.techsupportNA@nvent.com