Solution Summary: Worker Rotation
Worker rotation is an administrative control that involves moving workers to different jobs periodically within a shift. On any given worksite, there are certain tasks that are more stressful and require more energy than others. Often, these are the tasks that lead to overuse injuries. The extra stress could be associated with repetition, overhead or stooped posture, or excessive amount of force necessary to complete the task. Worker rotation differs from other engineering controls in which the working environment or tools are altered. Worker rotation does not change how the work is done, but spreads the workload of the task to many workers, instead of only a select few.
Description:
Worker rotation is an administrative control that involves moving workers to different jobs periodically within a shift. On any given worksite, there are certain tasks that are more stressful and require more energy than others. Often, these are the tasks that lead to overuse injuries. The extra stress could be associated with repetition, overhead or stooped posture, or excessive amount of force necessary to complete the task. Worker rotation differs from other engineering controls in which the working environment or tools are altered. Worker rotation does not change how the work is done, but spreads the workload of the task to many workers, instead of only a select few.
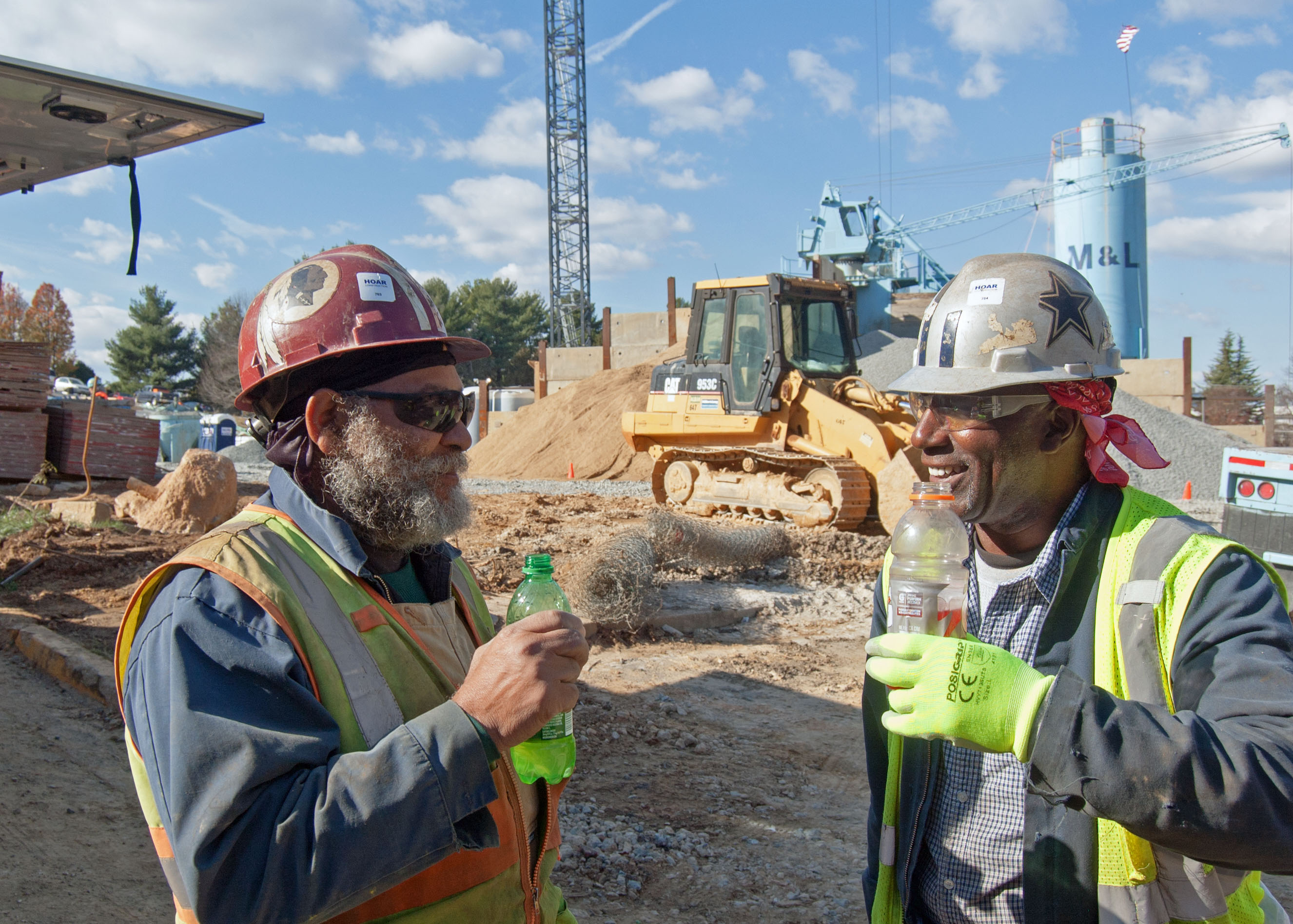
(Photo courtesy of ELCOSH)
Worker rotation works best when the jobs are distinctly different in terms of risk factors. For the best recovery of fatigue, jobs that require extra exertion should be alternated with less demanding jobs. An example of inappropriate worker rotation is alternating drilling overhead with lifting heavy cement bags; both tasks are physically demanding. However, alternating drilling overhead with low-intensity worksite clean-up would be appropriate. Similarly, workers should use different muscle groups in consecutive tasks. For example, workers could rotate between lifting tasks using low back muscles and use of power hand tools.
The first step towards implementation is designing the rotation schedule. First, the most stressful tasks should be identified. Next, the time it takes to cause fatigue performing these tasks should be determined. The length of time at each task station should be based on the most demanding task. Adequate rest periods should still be given when using a worker rotation.
A poorly designed worker rotation can actually increase worker stress levels. Worker rotation is not appropriate in the following situations:
- Tasks with extremely high risk of injury. The risk should be protected from the entire workforce. Training a select group to complete high risk tasks safely is a better alternative.
- Jobs/tasks that are extremely fatiguing for certain muscle groups should not be in included in a worker rotation, especially when followed by other tasks using the same muscle groups. Engineering controls and worker education on energy saving techniques are better alternatives.
Worker rotation is appropriate in the following situations:
- Tasks that cause fatigue after performing them for two or more hours.
- Tasks performed in fatiguing conditions (ie. extreme heat, humidity, or cold).
- Shifts longer than eight hours.
- Visually and attention demanding tasks, such as inspection.
Risks Addressed:
Musculoskeletal disorders associated with:
- Overhead work
- Stooped postures
- Manual materials handling
- Stressful hand and wrist activity
- Kneeling & squatting
- Repetitive work
How Risks are Reduced:
People participating in a worker rotation are still exposed to risk factors that could cause injuries. However, the length of exposure to the risk is decreased. For example, workers do not have to sustain awkward postures or be exposed to repetitive work for long periods of time.
Independent published studies report that there is a decrease in the risk of developing injury when a worker is exposed to a variety of tasks requiring different muscle groups and exertion levels. Studies also have shown that workers who perform repeated activities above shoulder level are at greater risk of sustaining shoulder musculoskeletal disorders. Workers who spend more time in stooped posture or other awkward back postures are at a higher risk for developing low back problems. Worker rotation is an effective intervention for reducing this time.
It should be remembered that worker rotation does not change the risk factors of a given task. The risk factors are distributed over more workers, but the risk of injury is still present.
Effects on Productivity:
Productivity is maintained or increased on a worksite with an effective worker rotation.
Additional Considerations:
Worker rotation can be effectively used for workers placed on light duty after returning from an injury. If a worker has limitations, the tasks they perform within the worker rotation can be altered.
Although worker rotation can be an effective intervention, implementation of engineering controls is usually a better solution for decreasing the risk of MSDs.
Availability
Guidelines for designing worker rotations can be found at:
- National Institute for Occupational Safety and Health www.cdc.gov/niosh
- Occupational Safety and Health Administration www.osha.gov
Return on Investment
To calculate the return on investment (ROI) for your specific application, please visit our Return on Investment Calculator. While a specific ROI example has not been developed for this particular solution, the ROI Calculator provides a useful tool and guidance on how to generate your own on investment analysis.